شرکت برنا گستر پارسی - سازنده ماشین آلات تولید آجر
- k
- v
- n
- z
- i
- x
- m
- e
- t
- a
- x
- l
- 4
- 0
- 4
- y
- y
- w
- v
- b
- o
- q
- d
- y
- p
- a
- p
- a
- g
- e
- v
- j
- a
- n
- o
- t
- s
- c
- e
- w
- v
- x
- e
- p
- c
- f
- h
- q
- e
- f
- o
- u
- n
- d
- s
- w
- q
- v
- o
- s
- m
- v
- f
- u
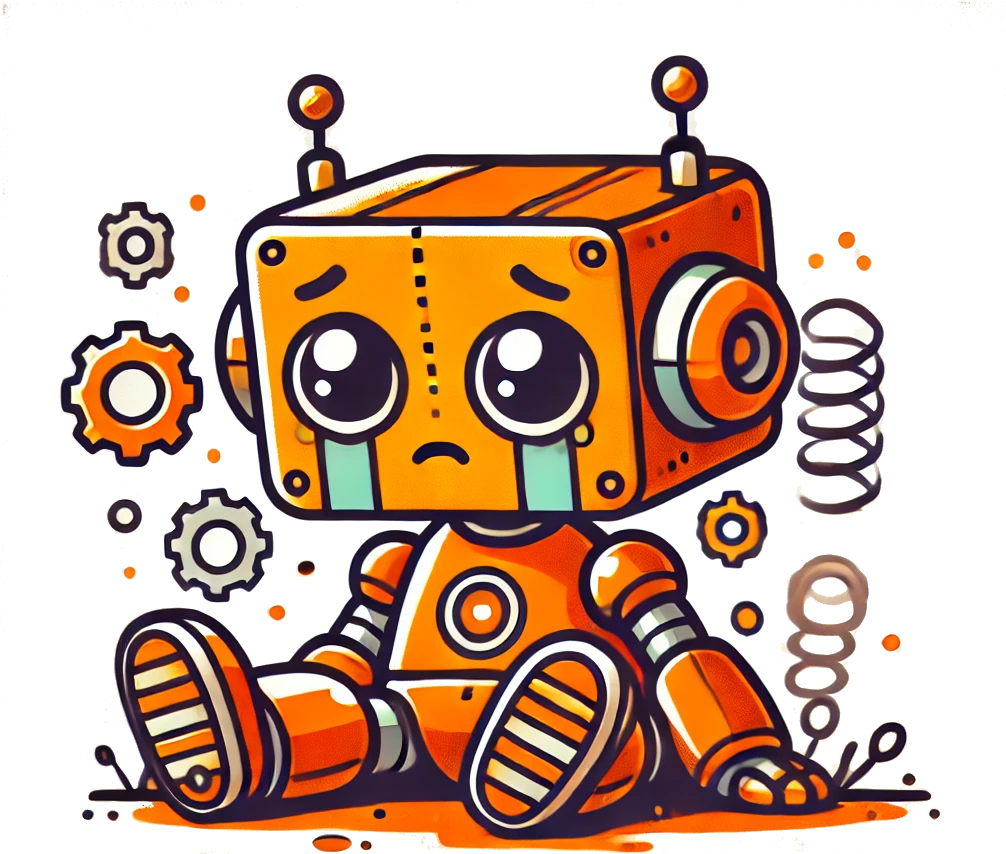
صفحهای که دنبال آن بودید پیدا نشد
متأسفانه صفحهای که به دنبال آن بودید پیدا نشد. ممکن است بهطور موقت در دسترس نباشد، جابجا شده باشد یا دیگر وجود نداشته باشد.
آدرس وارد شده را بررسی کنید و دوباره تلاش کنید. همچنین میتوانید در بخشهای دیگر سایت ما نگاهی بیندازید.